Introduction
In today’s rapidly evolving technological landscape, machine vision systems play a pivotal role in various industries, enabling automated visual inspection, quality control, and precise measurements. These systems leverage advanced imaging techniques to extract valuable information from images or video streams. In this article, we will delve into the main components of a machine vision system, exploring their functions and highlighting their importance in achieving accurate and reliable results.

1D Vision Systems
1D vision systems, also known as line scan systems, are a fundamental component of machine vision. These systems capture images line by line, enabling high-speed scanning of objects or scenes. The core element of a 1D vision system is the line scan camera, which consists of a linear array of photosensitive elements. As the object moves past the camera, each element captures a single line of the image, which is then combined to form a complete image.
To ensure optimal performance, 1D vision systems require precise synchronization with the moving object or conveyor belt. This synchronization allows for accurate image acquisition, minimizing motion blur and distortion. Additionally, specialized illumination techniques, such as strobe lighting, are often employed to enhance image quality and improve the visibility of the object’s features.
2D Vision Systems
2D vision systems are another integral part of machine vision, offering the capability to capture complete images of objects or scenes. These systems employ 2D cameras equipped with an array of photosensitive elements arranged in a grid-like pattern. By capturing the entire scene at once, 2D vision systems provide a more holistic view, facilitating tasks such as object recognition, defect detection, and barcode reading.
The key advantage of 2D vision systems lies in their ability to extract detailed spatial information from the captured images. This information enables precise measurements, such as length, width, area, and position of objects. To optimize image quality, 2D vision systems often utilize various imaging techniques, including lens selection, aperture control, and image preprocessing algorithms, to enhance contrast, sharpness, and overall clarity.
Area Scan vs. Line Scan
When considering the selection of a vision system, it is essential to understand the distinction between area scan and line scan technologies. Area scan cameras capture a complete 2D image at once, making them suitable for stationary objects or scenes. These cameras excel at tasks requiring high resolution and accurate color representation, such as product inspection or facial recognition.
On the other hand, line scan cameras are more suitable for applications involving continuous movement, such as web inspection or conveyor belt sorting. By capturing images line by line, these cameras mitigate motion-related artifacts and enable high-speed imaging. Line scan technology is particularly useful when inspecting long objects or surfaces that cannot be entirely captured in a single frame.
The choice between area scan and line scan cameras depends on the specific requirements of the application, considering factors such as object size, speed, and the need for continuous inspection.
3D Vision Systems
In certain applications, the ability to perceive depth and reconstruct three-dimensional structures is crucial. This is where 3D vision systems come into play. These systems utilize various techniques, such as laser triangulation, structured light, or stereo imaging, to capture depth information and generate accurate 3D models of objects or scenes.
3D vision systems employ specialized cameras or sensors that capture depth information in addition to traditional 2D images. By analyzing the disparity between corresponding points in multiple images or using the known properties of projected patterns, these systems can precisely determine the depth of various points within the field of view.
The applications of 3D vision systems are vast, ranging from industrial automation, robotics, and autonomous navigation to medical imaging and virtual reality. These systems enable accurate measurements, shape analysis, and object recognition in complex and dynamic environments.
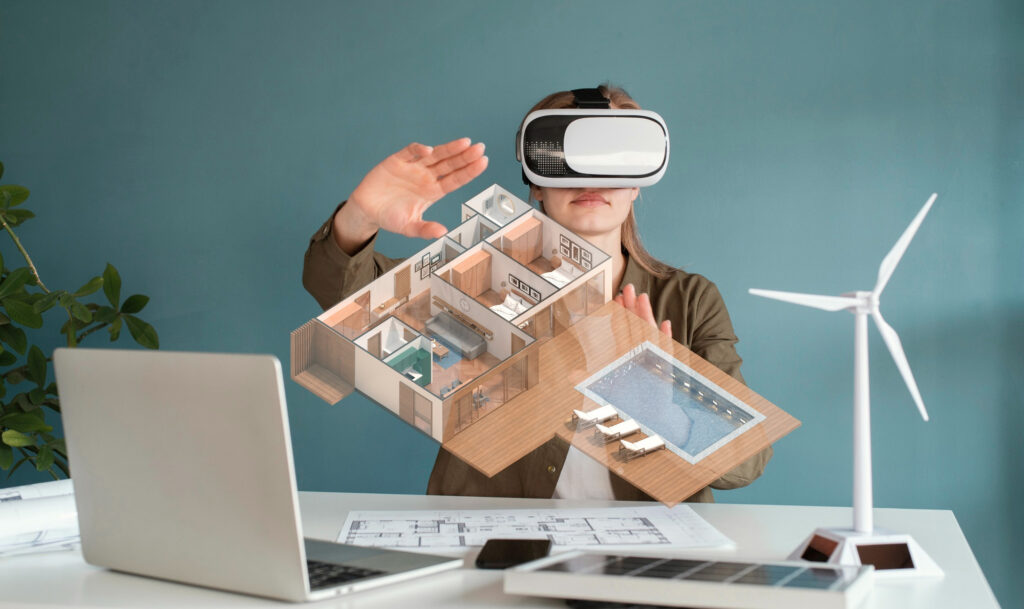
Conclusion
Machine vision systems encompass a diverse range of technologies, each serving a specific purpose in achieving accurate and reliable visual inspection. From 1D and 2D vision systems to area scan and line scan cameras, and the advanced capabilities of 3D vision systems, the components of a machine vision system work together to extract valuable information from images or video streams.
Understanding the capabilities and limitations of each component is crucial when designing and implementing a machine vision system. By leveraging the appropriate components and optimizing their performance, organizations can enhance product quality, increase efficiency, and achieve a competitive edge in today’s fast-paced industries.