Machine vision is a rapidly evolving field that combines various technologies to enable automated visual inspection and analysis. The effectiveness of machine vision systems relies on the seamless integration of different components, each playing a crucial role in the overall functionality and performance. In this article, we will delve into the key components of machine vision, exploring their significance and how they contribute to the success of such systems.
Lighting
Lighting plays a fundamental role in machine vision applications as it determines the quality and clarity of the captured images. Proper illumination is crucial to ensure accurate detection, identification, and analysis of objects within an image. Different lighting techniques, such as bright-field, dark-field, backlighting, and strobe lighting, are utilized based on the specific requirements of the application.
The choice of lighting depends on factors such as the surface characteristics of the objects, the desired contrast, and the inspection environment. The proper positioning and configuration of lighting elements, including LEDs, fiber optic lights, and diffusers, are critical in minimizing shadows, reflections, and unwanted noise in the acquired images.
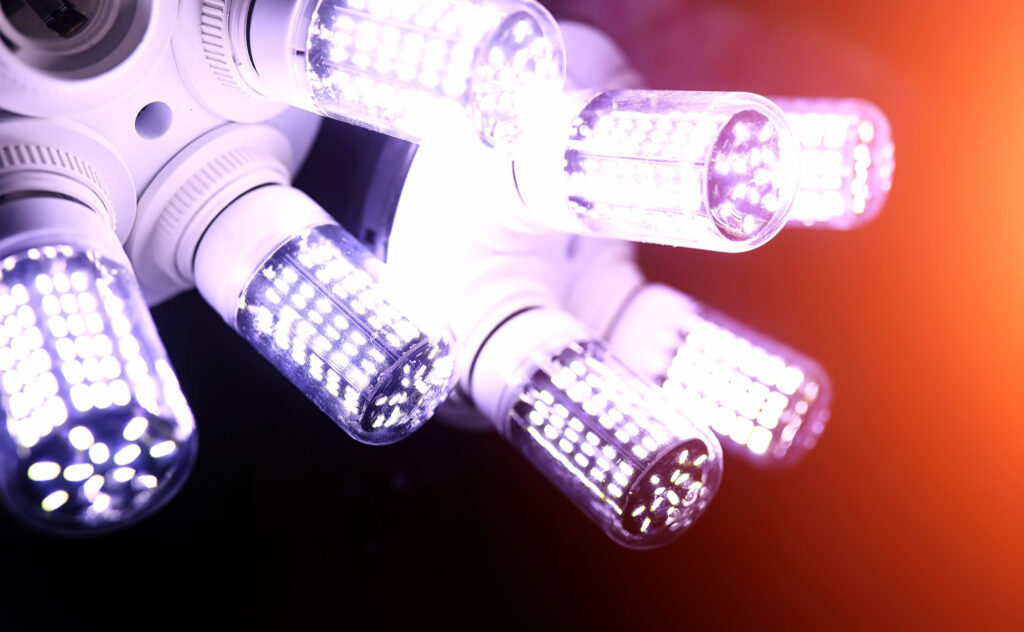
Lenses
Lenses are essential components in machine vision systems that determine the clarity, field of view, and depth of field of the captured images. They focus the incoming light onto the image sensor, ensuring that the objects are accurately represented. Machine vision lenses come in various types, including fixed focal length lenses, zoom lenses, telecentric lenses, and macro lenses.
The choice of lens depends on the application requirements, such as the working distance, object size, and desired image resolution. High-quality lenses with low distortion and good light transmission properties are preferred to achieve accurate measurements and precise analysis.
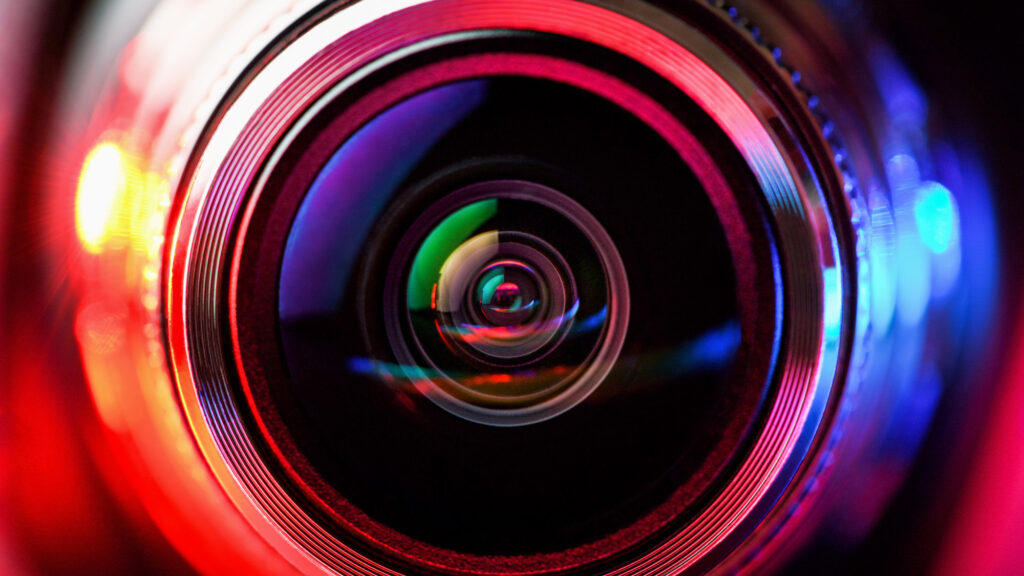
Vision Processing
Vision processing refers to the algorithms and software used to analyze the images captured by machine vision systems. This component plays a vital role in extracting meaningful information from the images and making intelligent decisions based on that information. Advanced vision processing techniques, such as pattern recognition, edge detection, color analysis, and feature extraction, enable the identification of defects, classification of objects, and measurement of dimensions.
Powerful processors and dedicated hardware, such as graphics processing units (GPUs) and field-programmable gate arrays (FPGAs), are employed to perform real-time image processing tasks. Machine learning algorithms, including deep learning and convolutional neural networks (CNNs), have also gained popularity in enhancing the accuracy and robustness of vision processing.
Image Sensor
The image sensor is a critical component that captures the optical information from the scene and converts it into electrical signals. CMOS and CCD are the two primary types of image sensors used in machine vision systems. CMOS sensors are known for their low power consumption, high-speed operation, and integrated functionalities, making them suitable for real-time applications. CCD sensors, on the other hand, offer better image quality and sensitivity, making them ideal for applications that require high-resolution and low noise.
The selection of the image sensor depends on the specific requirements of the application, such as the desired image resolution, frame rate, and sensitivity. Factors such as pixel size, dynamic range, and signal-to-noise ratio should be considered to ensure optimal image quality and performance.
Communications
Communication plays a crucial role in machine vision systems, allowing the transfer of data between different components and facilitating seamless integration with other automation systems. Various communication interfaces, such as Gigabit Ethernet, USB, Camera Link, and CoaXPress, are commonly used in machine vision applications.
The choice of communication interface depends on factors such as the required data transfer rate, distance, and compatibility with other system components. Ethernet-based interfaces, such as GigE Vision and USB3 Vision, offer flexibility, scalability, and ease of integration, while specialized interfaces like Camera Link provide high-speed and deterministic data transfer capabilities.
Conclusion
Machine vision systems are composed of several interconnected components that work in synergy to achieve accurate and reliable visual inspection and analysis. Understanding the significance of each component, including lighting, lenses, vision processing, image sensors, and communications, is crucial in designing and implementing effective machine vision solutions.
By carefully selecting and optimizing these components based on the specific application requirements, it becomes possible to achieve superior image quality, precise measurements, and real-time analysis. Stay updated with the advancements in machine vision technology to leverage the latest innovations and push the boundaries of automated visual inspection and analysis.